SwipeGuide
Improve Digital Standards with SwipeGuide Checklists
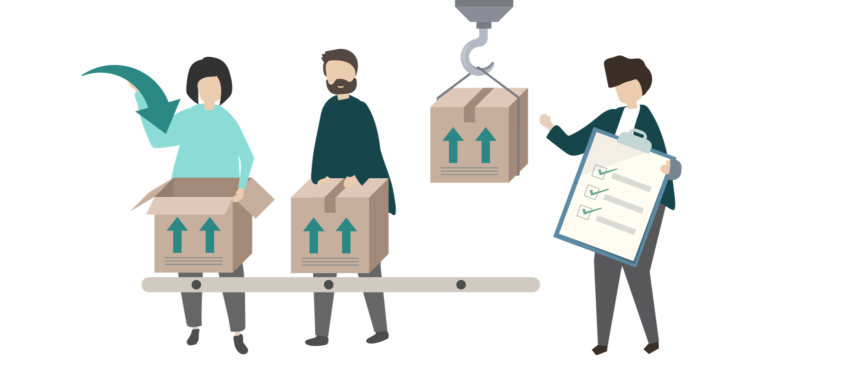
Has work been performed according to your standards? Our new Checklists feature allows manufacturers to capture more operational data from inspections, audits, and Gemba Walks on the factory floor or in the field.
Our latest feature leverages the user-focused design principles of the SwipeGuide platform and empowers teams to create and share comprehensive checklists within the app.
Users swipe through a highly visual digital checklist and indicate the state of the production environment with a series of yes or no questions, supported by photos of the desired outcome. Supervisors integrate Checklists into their existing work instructions and add relevant feedback to facilitate continuous improvement throughout your global operations.
What you get:
- Custom digital visual checklists
- Integration within your existing Guides
- Drag-and-drop creation and intuitive editing
- Integration with your existing SwipeGuide analytics dashboard
- Easily deliver instant visual and text feedback on checklist results
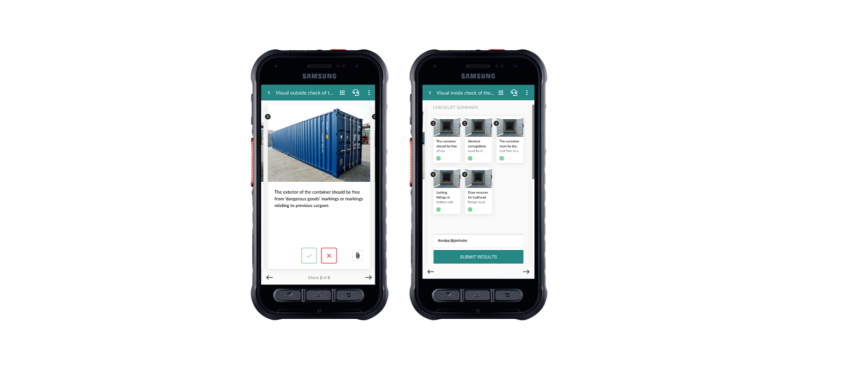
Successful manufacturing depends on a company’s ability to continually assess and improve their processes and procedures. But how are these standards actually enforced and improved throughout day-to-day operations? It’s one thing to deliver high quality work instructions and SOPs to your frontline workers. It’s an entirely different challenge to make sure that your workforce adheres to these standards in a way that promotes accountability and growth.
Industry experts agree that the most practical and productive way to enforce standards and capture critical operational data is for supervisors to be physically present in the production environment. This means combining traditional audits and quality control inspections with lean improvement techniques such as Gemba Walks.
These checks deliver the following benefits:
- Monitor adherence to industry and company standards
- Capture deviations from norms and offer corrective action
- Capture improvements to existing processes and procedures
- Inspire accountability by leading by example
But in the fast-paced world of industry 4.0, these methods need to leverage the power of a comprehensive digital solution to keep pace with the scale of modern manufacturing. The world’s top companies already have plans to use our new Checklist feature to digitize quality control and audit checklists to increase the productivity and insights gained from their factory floors.
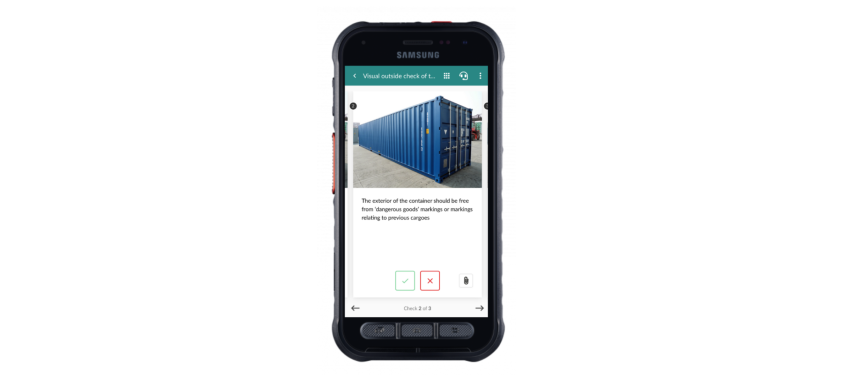
Same design, same intuitive process.
The checklist feature operates on a simple premise: content creators and supervisors use our intuitive drag-and-drop interface to craft minimalist checklists that tap into the principles of how people really work and learn on the job. It’s just a matter of writing what needs to be included in the checklist and uploading a visual cue of what to look for.
Users simply swipe through a highly visual digital checklist and indicate the state of the production environment with a series of yes/no questions, supported by photos of the situation in question. Are safety standards up to par? Is the line properly sanitized? Has maintenance been correctly performed?
These checklists are linked to the digital work instructions and SOPs that teams are already using on the shop floor, allowing each audit, inspection, and Gemba Walk to be directly connected to the task at hand and be as relevant as possible. High quality photos and minimalist text eliminate the opportunity for confusion, and provide a concrete reference point to users.
Like all of our features, Checklists are available on rugged mobile and wearable devices. Insights are more relevant - and discussions about improvements are more impactful - when inspections and audits can be performed directly in the production environment.
Capture detailed analytics and empower a feedback loop.
Just like our work instructions and SOPs, every result from your checklist will be immediately stored in your comprehensive analytics dashboard. This allows supervisors to investigate trends, monitor deviations, and gather insights to facilitate continuous improvement.
Checklists provide an invaluable opportunity to capture ideas and information about potential process improvements. Supervisors can leave detailed feedback on each checklist result in the form of comments and photos, effectively digitizing the feedback loop. These insights are essential for manufacturers to scale improvements across a complex global value chain.
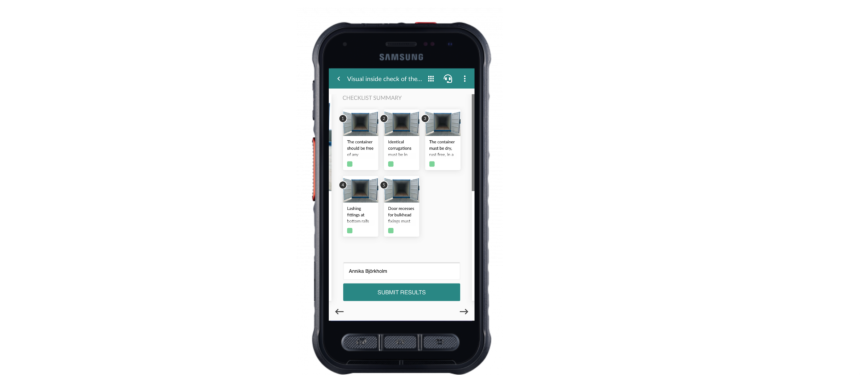
The next steps in workforce excellence.
Standard work allows manufacturers to consistently deliver excellence throughout their daily operations. The Checklists feature enhances this principle by delivering an intuitive, future-proof, and data-driven solution to capturing crucial operational data . But it also leverages our user-focused design philosophy to create a meaningful digital dialogue about continuous improvement.
SwipeGuide’s mission is to empower manufacturers to tap into the expertise of their experts - and often these experts are the frontline workers on the factory floor. Simply put, the Checklist feature allows manufacturers to use real data and crowdsourced knowledge to facilitate improvements in their daily operations.
Interessante informatie?
Het netwerk van de Lean Portal.nl is altijd benieuwd hoe we verder kunnen helpen.